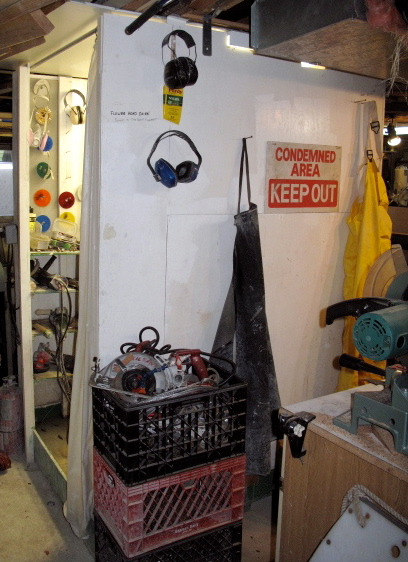
The Wet Carving Box
and
How to Carve in Small Places
For over a decade, I’ve worked year round in my basement wet carving stone. I have constructed a small work place to eliminate the dust, contain the water, and work in the comfort of a controlled environment. This presentation is an introduction to what I have done to arrange my space, photos of work spaces by others, and the wet tools that I use. If available, I use wet tools that are designed for wet use. Skill saws, and die grinders have yet to be made with water feeds. On all of my tools I use controlled application of water to the abrasive blades and wheels to both control dust and prolong the life of the abrasive tool. See my overview of my tool list at end of this article.
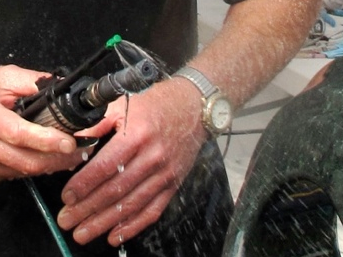
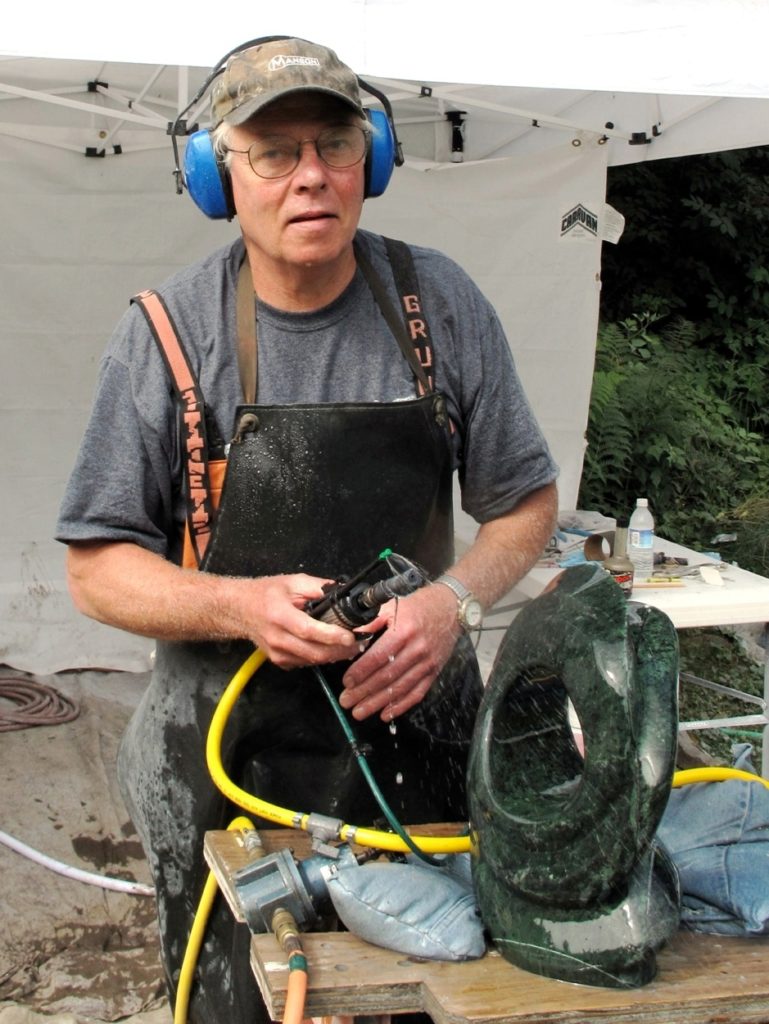
Pat Barton August 2013
For a printable PDF version [CLICK HERE]
Expanded Example of Water Recirculating System PDF
Why you work wet: Silica Dust Poses Health Hazard in Stone Fabrication Industry – Silica Dust PDF
![]() |
![]() |
![]() |
![]() |
![]() |
![]() |
![]() |
![]() |
![]() |
![]() |
![]() |
![]() |
PARTS LIST for MISTER
Schematic diagram of how a mister addition is put together
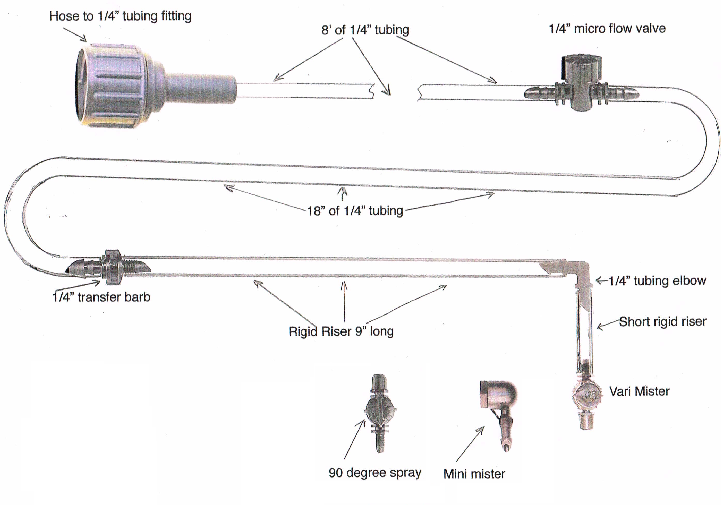
Drip irrigation part suppliers
I have only used “dripworks” misters. I have had very good service from them. Below are the web links to the parts in the diagram.
90 degree mini mister
Vari Mister (with valve)
Rigid riser (I use the 12”)
Tube to riser connector
Elbow for tubing
Micro valve
Hose barb to tubbing fitting
Tubing
90 degree sprayer
Most of the above parts must be ordered on groups of 5.
Home Depot and other stores have most of the drip irrigation parts, but they don’t have the any mister parts. I have used some of their sprayers. Their 90 degree sprayers work best. Some of these sprayers come on a rigid riser with a separate plastic stake.
How do you attach the drip system to your tool?
I use nylon zip ties.
You can also use velcro cable raps. Cinching type works the best.
Or you can use electrical tape. Grooved wood blocks, glued to your tool, will help hold the riser tube in place.
To make certain your tubes and riser connections do not leak I recommend: permatex with-ptfe
Gasket sealer can alo be found at auto parts stores. Without it I have had some leakage.
TOOL FOR GRINDING AND WORKING WET
The below list of tools shows some of the power tools that are available to stone sculptors. Many are manufactured with center water feeds, GFCI protection, and are designed for wet use. If available, I use wet tools that are designed for wet use. Skill saws, and die grinders have yet to be made with water feeds. On these tools I use controlled application of water to the abrasive blades and wheels to both control dust and prolong the life of the abrasive tool. The number of tools that are now being manufactured for wet use demonstrates the demand for water supplied tools that use diamond blades and other abrasives. I. GrindersA. Right Angle Grinder. 7,000 to 10,000 RPM 1. Comes two general sizes. 4 to 5”, and 6 to 9”. 2. Has 5/8’-11 threaded shaft. a) Allows use of grinding wheels. b) Allows use of diamond circular saw blades. c) Care must be taken to not exceed the RPM requirements of the wheels and blades. d) These grinders are too fast to use diamond velcro polishing pads. The high speed will throw the pads off the backer pad. 3. Right Angle Electric Grinders a) Uses standard electrical power. b) Quieter than air grinders. c) Danger of electrical shock. (1)Always use GFCI circuits. (2) Most factory wet grinders have GFCI protection. d) Motor windings can be damaged by stone debris. e) Come in both dry and water supplied models. (1) Dry models are very common. (2) Wet models are expensive Come with center water feed. f) Constant speed or variable speed. 4.Right Angle Air Grinders a) No danger from electrical shock. b) Small and light weight when compared to electrical. c) Requires a large compressor. d) Loud. You must always use hearing protection. e) Come both wet and dry. Dry is most common. f) Easy to add water to these tools. B. Die grinders. 1. They use a large variety of tools. For grinding, sanding and polishing. 2. They are available with 1/4”, 6mm, and 1/8” collets. 3. Electric die grinders a)Usually are straight grinders. b) Variable speed. c) Uses standard electrical power. d) Must be protected by GFCI protection if used wet. e) Motor windings can be damaged by stone debris. f) Expensive. 4. Air die grinders. a) Require a large compressor b) Come in both straight and right angle. c) Speed easily controlled with a regulator. d) Easy to install wet sprayers to tools. e) Loud. Must use hearing protection. C. Right Angle Grinder / Polishers, have speeds less than 5000 RPM. 1. Both electric and air. 2. Available with center water feed. 3. Electric grinder / polishers. a) Must use GFCI protection if used wet. b) Uses standard electrical power. c) Most are variable speed. d) Most have center water feed. e) Most have splash guards. 4. Air grinder / polisher. a) Requires a large compressor. b) Loud requires hearing protection. c) Most have center water feed. d) Lighter and smaller than electric units. Fits into tighter places. e) No shock hazard. f) Speed controlled by regulator. II. SawsA. “Skil” type saws. Electric saw. 1. Worm drive or direct drive. a) Worm drive saws usually have the blade on the left of the saw. b) Direct drive saws have the blade on the right of the saw. 2. A dry tool used in wood working and construction. 3. Motor windings can be damaged by stone debris. 4. Electrical shock. Always use GFCI protection. 5. Water can be applied to the blade to cool and flush debris. 6. 7-1/4” is the most common size. 7. These saws are very good for cutting frets on large surfaces. B. Hand held tile saws 1. Small blade size. 4” 2. Wet 3. Electric C. Diamond cut off saws. 1. Hydraulic, electric and gasoline powered. Gas powered is the most common. 2. Uses 12” to 16” diamond blades. 3. Most units have water fixtures for the blade or kits to apply water. 4. Can be used dry with a dry cutting diamond blade. 5. Must be used outside because of exhaust fumes. 6. Very loud. D. Diamond chainsaw. 1. Hydraulic and Gasoline powered. 2. Expensive. 3. Comes with water fixture. Must be used wet to prevent chain and bar damage. E. Diamond ring saw. 1. Hydraulic and gasoline powered. 2. Expensive 3. Comes with water fixture. Must be used wet. III. Core drilling machines A. Uses standard electrical power. 1. Must be GFCI protected 2. Loud, use ear protection. B. Hand held. 1. Water fed through center of bit. 2. Requires lots of pressure to feed drill. Very tiring. 3. Must be guided carefully and in line. 4. Largest bit that can be used is 6”. Really 4”. 5. Expensive. Both bits and drill. 6. Very useful. C. Drill press type stand mounted. 1. Can use bits up to 10”, larger with spacers. 2. Both the drill rig and the stone must be held securely. 3. Water fed through center of bit. 4. Pressure is easy to apply with drill press. 5. Drill press mast guides bit and cut correctly if secured. 6. Expensive. 7. Very useful D. Wet right angle grinder with diamond core bit. 1. Variable speed grinders work best for core drilling. 2. Many core bits have recessed threads that won’t allow for a proper connection to the grinder. 3. Works well for small core holes for pins. |