The following is an interview with Hank Nelson. He has been a member of NWSSA since the 1980 ‘s when Meg Pettibone held NWSSA meetings. in her little studio in the Fremont District of Seattle. Many of us know Hank as a facilitator of power equipment at the Camp Brotherhood Symposium.
WL: You’re one of the old timers, aren’t you. Then you’ve been at all the symposiums since 1987?
HN: I have been at every symposium at Camp Brotherhood since 1991.

WL: What started you becoming interested in sculpting? (We are walking back through innumerable pieces of stone equipment, metal equipment, a five-ton press, and drill presses.)
HN: In 1979 I was living in Santa Fe and I built my own adobe and stone house. I have always been interested in viewing sculpture. It had never occurred to me that I might be interested in making it. After I completed the house, some of my friends said it looked very much like a sculpture. I was going to go on to construction but the construction market fell. So I signed up for a ceramic course at UNM in Albuquerque. They didn’t have a slot open so they put me in a sculpture class. That was in 1981 and that whetted my interest.
WL: So you started with clay as your original medium.
HN: Clay and wood, some small pieces of soapstone, and it evolved from there.
WL: What kind of art training did you have other than that?
HN: I never had any formal art training. My field was anthropology. In 1984 I lived in Italy for four months and a Dutchman taught me stone carving.
WL: From the looks of your yard here, I see primarily granite. You said when you first started, you did a few pieces in soapstone. Can you give me some idea how it evolved into working with granite.
HN: Let’s take a walking tour and I’ll show you.
WL: (We are going inside his huge building.) Hank, this is the dream of everybody to have a building this size to work in.
HN: This has been my dream for fifteen years. I finally built it three years ago. It will allow me to do my stone work outside and steel fabrication inside when I get totally set up. I’m going to have welding both inside and outside. I would like to forge and continue to cast.
WL: (We are walking through innumerable pieces of stone equipment, metal equipment, a five-ton press and drill presses.)
HN: My first piece in Italy was a Carrara ordinario marble. It started out as a 1200 lb. piece. After two or three months of working and learning on it, it was probably about a 700 lb. piece.
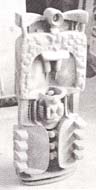
WL: How did you see the image that came out of this stone?
HN: I made a clay model. It was totally different than this. I finished roughing the stone out, boxed it up and brought it back home with a container of stone. Finally I realized I had to complete it. At that point, after several years absence from it, I had to redesign it. The original design didn’t work.
WL: It’s a very organic shape with many openings and interlocking forms. It stands close to 30″ tall and it is about 24″ across in one dimension and about 18″ across in the other dimension.
HN: A lot of my work is unfinished. I have a hard time finishing things because I want to go on to something new.
WL: Do you eventually come back to the piece?
HN: Eventually I come back, but three-quarters of what I started remains unfinished.
WL: Why?
HN: I find it really mundane. I have a hard time going back and doing the final steps in stone-the polishing. For me there is nothing creative in that. I want to get on to something else.
WL: You spend all of the time trying to be the perfectionist?
HN: Yes, in finishing and going through all the sanding stages and polishing.
WL: What you need, Hank, is to have a young apprentice. You teach him and in payment he has to do your finish work for you. You supervise him. Many of the old sculptors did that.
HN: That’s something I would give anything for. In working with the UW art foundry, a friend of mine, Norm Taylor, a professor at UW, took me aside and suggested I do casting. So I spent the next five years doing casting. Loved casting. I still love it. It’s something I want to get back into and incorporate with my stone.
WL: (What Hank is showing me right now are some very tall, skinny, totemic-type forms. They have faces and an inference of a human form. It reminds me very much of the things I have seen illustrated from New Guinea and also from Africa.) Where do you get the ideas to start with, Hank?
HN: I relate and respond to African art. I love the Parisian African art museum but, while I appreciate a great many sculptors, I don’t think that I have been able to adopt any of their imagery. On all of my cast iron work, it has evolved while I’m working on the piece. I have a general idea of what I want to do in carving it. These are all carved in negative in chemically-bonded set sand. They take hundreds of hours to carve and then I have a negative image in the sand which in turn, when I cast it, f come up with a positive image.
WL: Going from this iron work and the big totemic columns, some of-your ideas are starting to show in your stone work, too. Speaking about stone, what type of tools did you start with?
HN: With soapstone, I used a file, a knife, and sandpaper.
WL: Then when you went to Italy, you were introduced to the marble tools and the various power tools?
HN: Yes, to all of the tools.
WL: Do you have a preference for which tools you use?
HN: Yes, I sure do have a preference. On that piece (pointing to the Utah oolitic limestone), I couldn’t have done that with any of the machine tools. Plus it’s a very easy stone to work by hand. That was done by hand chisels, files and sandpaper. On marble, I like to use a hand point to rough it out as well as a diamond saw, if that is appropriate. My favorite tool is the Cuturi air hammer. I generally use four or five gradinos which are the tooth chisels. In Italy it’s called the gradino. So I almost always use gradinos and a flat chisel. On granite, it’s a totally different process. My diamond blade is almost always the first step, then to granite hand tools. I think the machine I use the most on granite is my pneumatic hammer with bushing tools. And then after that I use various chisels.
WL: (Hank has all his tools laid out neatly in a row.) .
HN: I’ll use this big hand set all the time. They are all Trow & Holden which I think are fabulous tools. And then I go on to the ripper. This does a marvelous job in narrow places. When my bushing tools don’t do the job, I use this carving chisel.
WL: (One of the chisels has a heavy body on it. It’s a Trow & Holden pneumatic tool and it comes down to a fairly steep taper at the carbide tip. But the other one looks more like a marble tool in that its body tapers down to a very thin profile and it has not very much of a bevel on the carbide.) I would think that one would be quite fragile.
HN: No, it isn’t. I’ve done some amazing things with it.
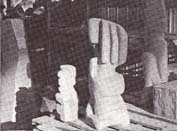
WL: (The carbide insert constitutes the first inch and a quarter in the tool, and then its socketed into the steel differently than I’ve ever seen.)
HN: These are tools that I have not used yet. This is a drill.
WL: A double-edged star drill.
HN: It’s similar to that. (It’s curved as a rondel.)
WL: That’s a nine-inch flush-cut. It’s the first time I’ve seen one. It’s neat. It has eight bolts holding it down.
HN: It’s an incredible blade. This is my four-and-a-half inch diamond grinding wheel (diamond cup wheel) and that is my seven inch. This is a Craftsman. I decided to try one because it has a five-year warranty.
WL: It looks like you’re working most of your stone dry.
HN: Yes. I want to start working wet in so far as my granite polishing. This is my one inch Trow & Holden and my 1/2 inch Cuturi which I began carving with and that is how I carve all of my marble.
WL: (We’re looking at another of Hank’s in-work sculptures. This one is in siennese yellow marble.) Is that a modified female figure or just a play on curves and lines?
HN: It’s more of a play.
WL: I asked you where you get your ideas, and you said the idea and the form just kept coming to you as you were working.
HN : Yes, in the cast iron.
WL: What about stone?
HN: No, except for the first piece. For almost every one of them I have a preconceived idea. Sometimes I have a crude sketch to help guide me, but almost always, whether I have a sketch or not, as I get further into the stone, I realize I have to make a change here and there that I hadn’t contemplated in order to come up with what my preconceived idea was and it usually happens that it comes out slightly or quite a bit different than what I had originally envisioned. I have one piece back there that is my personal Buddha. I knew exactly what I wanted when I started it and I didn’t deviate. Usually I deviate. I get into the stone and I think it’s going to work out better if I make this cut or do something that I hadn’t planned on.
WL: So you never make a maquette, a model?
HN: No, except for the first piece of stone I carved in Italy.
WL: Can you describe this shop building?
HN: Yes, it’s a Blue Ribbon. It’s a 48′ x 72′ building with two walk-in doors and a 12 foot high overhead drive-in door. The purpose of the building is for me to be able to fabricate fairly large steel and iron pieces.
WL: At the present time it’s a totally open ceiling and it is about 24 feet high to the peak.
HN: It is 13 ft. to the top of the door and about 16 feet to the eaves. I had the problem of building shelves and making them substantial enough for all my heavy steel so I bought an old warehouse.
WL: That’s what we make our big white beginners’ tent with at Camp Brotherhood.
HN: This wonderful shelving will hold thousands of pounds and I didn’t have to build shelves into the walls.
WL: You’re always running at the symposium taking care of machinery. You never get a chance to carve.
HN: Well actually, starting last summer, I realized the symposium is an incredible resource. I don’t care if I do any carving. I wanted to be out there watching and learning and I think even more so next year. I’m not going to take a piece of stone. And if I find something there to whack away at, just for token’s sake, I might.
WL: You feel that by being involved in helping it run, that you share in everybody’s work and that you learn a tremendous amount?
HN: By getting involved in all the workshops~ they were just incredible last year-and hanging out at other people’s workstations. So for me, I can do my carving here and my learning there.
WL: How do you select your stone?
HN: I haven’t bought any marble since Italy. I didn’t know what I was doing at that time. I was a total novice. Now I’m finding that when I select my granite ~ I’m very interested in totemic imagery~1 am trying to find a way to do taller work such as I did in my cast iron. Some of the most recent pieces that I have done, came from dimensional stone such as that one over there (pointing to a piece of granite that is about 10″ by 8″ x 40″ long and another piece 12″ x 8″ x 48″ long). Until now I have been able to make one sculpture out of one block. What I’m going to do is take these two pieces and stand them upright and attach them together and that will constitute one sculpture.
WL: In other words, put one on top of the other?
HN: No, in width, in depth. And then either with this piece or the next, I will add in height. That’s going to be tricky.
WL: Yes, it is, but I’m sure with all the metal you have around here and all the methods you have, you will solve it very easily. (Pointing to piece illustrated on page 10. When I first looked at it, it looked like a triangular piece, but it is a rectangular piece mounted on a triangular piece of white granite and it is slotted with a saw and then portions have been carved back. This is Hank’s first totemic piece). So you’re going to continue this series?
HN: Yes, I am. I am finding that each one brings a whole new dimension for me to what I can do with stone. I really love working with granite. I like granite because of its durability.
WL: Now we can look at some of the other work. (This is a small totemic-type piece that stands 14 or 15 inches high.) How much more work are you going to do on it?
HN: I think it is just an experiment. Probably a model for a larger piece. And my fourth thing is this.
WL: (Each one he shows me is a little bit taller.) Describe it for me, Hank.
HN: It is about three feet high and about eight inches by eight inches. As I said, each piece that I do gels me a lot closer to knowing what I can do with granite, how far I can push it, how close I can come to working in the same manner that I work with my cast iron totemic imagery. Of course I am not trying to duplicate it precisely. I guess that is what I call pushing.
WL: What do you mean by pushing, Hank?
HN: By vast experimentation, by knowing how deep into a piece I can go and still maintain its structural integrity.
WL: How much time do you spend carving?
HN: Last summer I made a decision it was going to become fulltime for me. I’ve never sold anything. I’ve never even shown anything yet.
WL: Can you give me a statement of your philosophy–of life, of work.
HN: The visual urge to my endeavors is guided by my lifelong curiosity of how the animal kingdom and physical and spiritual matter relate to one another and to the larger universe and displaying this interaction. I am intrigued by the origin of human races and the variations and differences within each race. I seem to have a need to explore things of anthropological relevance. In so doing, it is important to integrate this work into the lives of those who are to live with it in a positive manner so as not to trample their spiritual and physical space with meaningless imagery of little or no substance. My work is my statement.
Similarly it remains untitled so that the viewer can formulate, without verbal guidance, a judgment and a relationship. Yet all of my work represents a specific being to me and in a rare situation I might title it.
Working stone for me is no more precious than working with steel, iron, dirt or carving styrofoam. Each material has its own inherent rewards and can accomplish different things. However, I find stone carving more difficult and therein lies the challenge of stone. Each move is critical to the success or failure of the piece.
My search for a spiritual path is heightened with the challenges of stone carving. A further challenge is coping with the inherent problems of carving. Of working monumentally and dealing with the logistics of handling and moving as well as scale. Philosophically. I feel like I’m not making any of these images to end up with another piece of work that is just going to take up space. I think, for me, it’s the working of the material that is important. When I go back to one of my earlier pieces, they are interesting but it’s history now. Sculpting assists me in my pursuit of a spiritual path.