Part of this material I used in the 20 hour granite course I taught at Pratt. Most of the info is from Tom Urban’s workshop at Camp Brotherhod, some from a workshop by Don Ramey that Hank Nelson organized at my place years ago. If you find anything useful, please add it to the article – Kirk
Grinders:
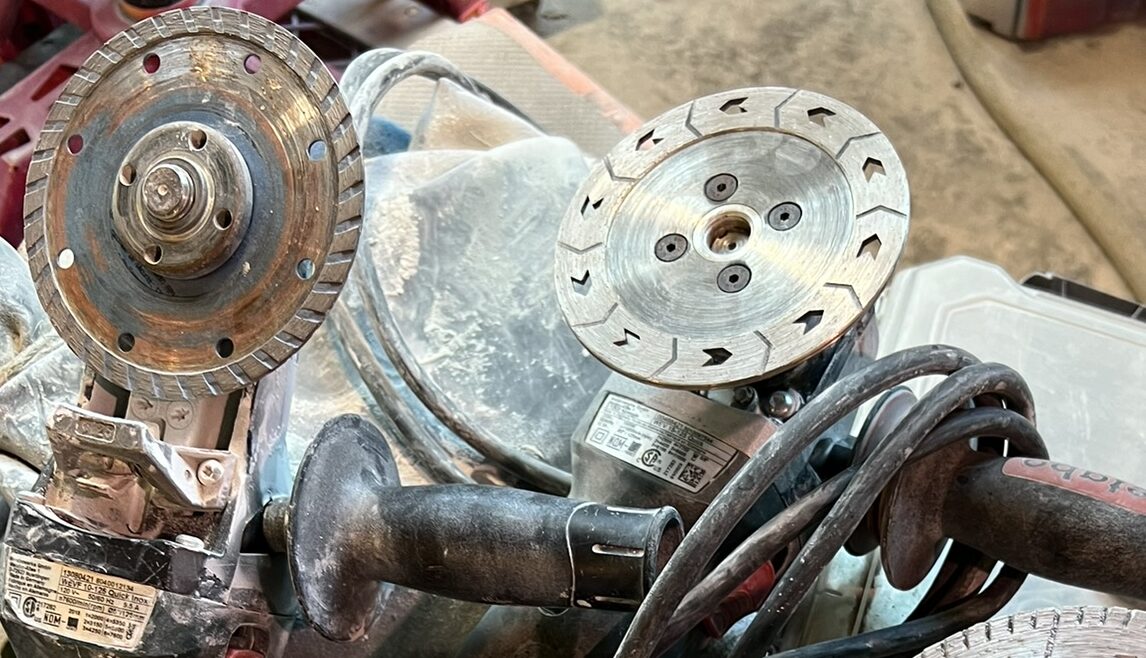
4-5 inch dry-cut diamond blades designed to run at about 10K RPM, which is speed of right angle grinders. For sufficient power, look for high 6 amp range or greater. Hitachi and DeWalt models hold up well. For variable speed, recommend Metabo or Makita. Avoid Bosch or Milwaukee. Larger blades (7-8 inches) run about 5K RPM, which is speed of 7-inch grinders or worm drive circular saws. Worm drive saws can be set up to run wet, keep blades cooler.
Grinder maintenance: Blow out grinders 2x daily. Blow outside, inside, and then blow out while running.
Diamond blades:
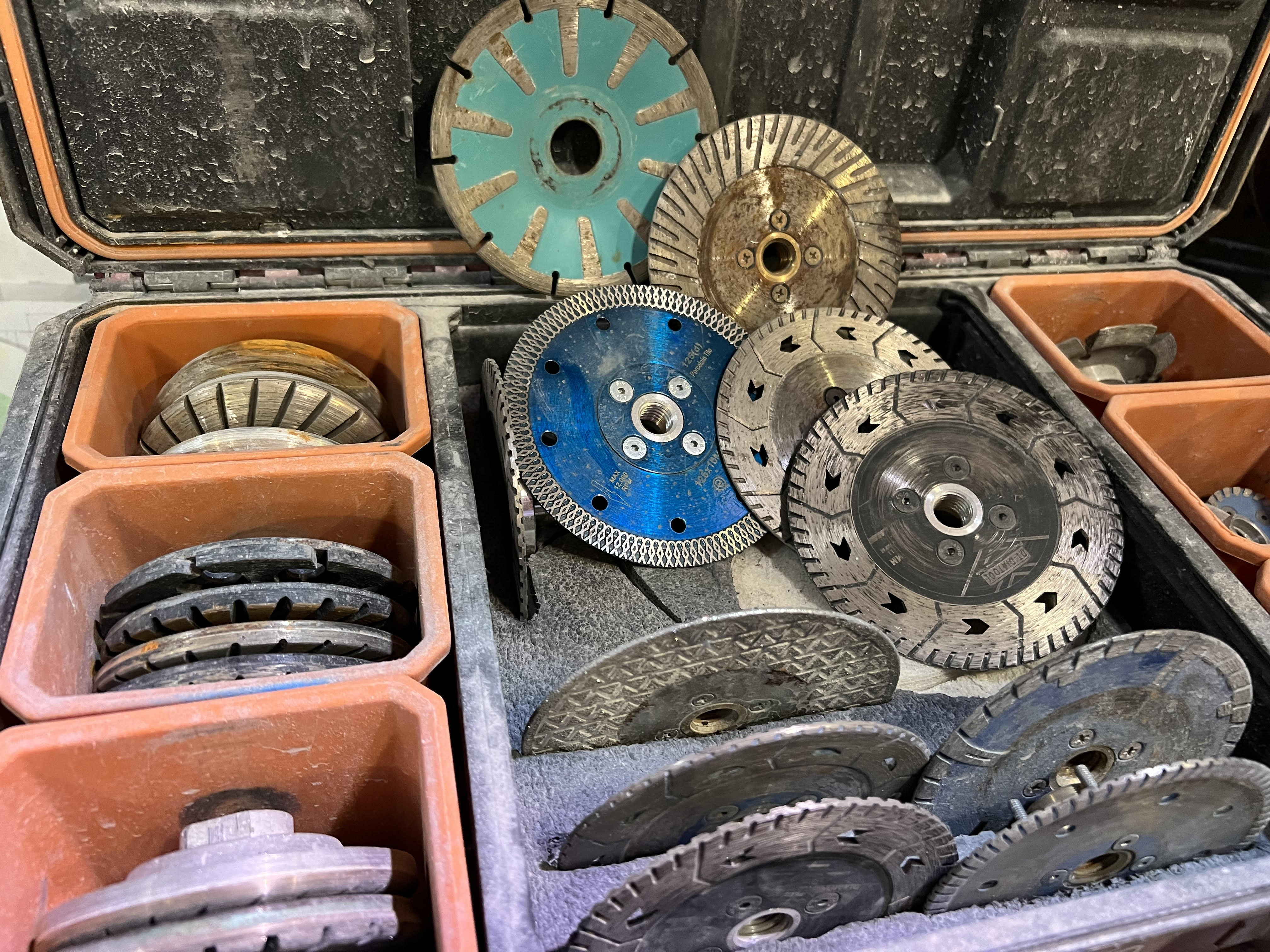
Turbo blades preferred. Mount blade so direction of turn matches direction on grinder. Segmented blades cut faster, but more chatter, more chance for segments to come loose. Blades with holes near the edge tend to cool better than ones with ridges going into core. Granite blades have different matrix than marble, wear differently—important to get right type. Cheap blades are usually inadequate, Alpha and Pearl are good quality blades. Blades can become glazed through use and need to have matrix opened to expose new diamonds (sometimes true for new blades). Tom Urban from U of O recommends cutting into cement block, then red brick as best method to open blade.
Roughing out:
Cut without forcing blade. Cut from left to right so direction of blade turn is into cut. Less tendency to kick back. If it does kick doesn’t go far. Take saw out of cut for return. Trow & Holden recommend letting blade cool by backing off pressure every 10-15 seconds and letting run up to speed. Take cuts down to about 1-2 inches.
Separation of cuts (fret thickness) determined by depth of cut; the shallower the cut, the closer together they should be placed. Frets broken out by hand hammer and point or chisel (T&H will grind beveled edge on offset hand set) or with air hammer and rough out machine chisel. Next set of frets can go at right angle, shallower & closer together. Use oblique light to see if saw kerfs all come to desired surface before popping out fins last time.
Saw safety
- Use guard with saws and diamond cup wheels.
- Always work with handle on grinder.
- Check blade for cracks before use.
- Don’t stand in line with blade during use.
- Don’t force blade into material, allow it to cut at own speed.
- Avoid long continuous cuts, allow blade to cool. Chattering in cut indicates overheating.
- Cut at right angle to surface, being careful not to twist blade in cut. Cut in straight line
- Cut so direction of blade turn is into cut.
- Do not plane with blades. Flexing of blade can stress & break core.